views
In the expansive universe of IT Hardware, few components are as versatile and essential as the Interface Module. Whether embedded in a control panel or acting as a bridge between devices, the interface module ensures seamless communication between various parts of a system. These modules are foundational to countless computer hardware environments, from industrial automation to telecommunications and data centers.
An interface module enables a device to communicate with another using defined protocols, voltage levels, and physical connections. This key piece of IT hardware acts as a translator, buffer, and regulator, ensuring that different systems can work together harmoniously without interference or signal loss.
The Importance of Interface Modules in Computer Hardware
Modern computer hardware systems are made of several interconnected components, each with specific functions. These include CPUs, memory, I/O devices, storage units, and networking interfaces. While they serve different purposes, they must all communicate effectively to form a cohesive and productive system.
Here’s where interface modules play a crucial role. By managing the input and output flow between subsystems, they ensure that signals are correctly interpreted, timing is synchronized, and data integrity is preserved. This is especially important in environments that use different communication protocols or electrical standards.
Core Functions of Interface Modules
1. Signal Conversion
Interface modules can convert analog signals to digital and vice versa. This is vital for integrating legacy devices with modern digital systems. For instance, in industrial IT hardware, analog sensors often need to communicate with digital PLCs.
2. Protocol Translation
Different systems use different communication protocols like RS-232, RS-485, Ethernet, Modbus, or CAN. Interface modules translate data from one protocol to another, ensuring compatibility and reducing communication errors.
3. Electrical Isolation
Many interface modules offer electrical isolation to protect sensitive computer hardware from voltage spikes or signal interference. This reduces the risk of damage and improves operational reliability.
4. Data Formatting and Buffering
Data transmitted from devices may not be in a compatible format for the receiving system. Interface modules reformat data and buffer it to manage timing mismatches or transmission delays.
Types of Interface Modules in IT Hardware
1. I/O Interface Modules
Input/Output (I/O) modules are perhaps the most common type. These modules connect sensors, switches, relays, and actuators to control systems. They are the bridge between the physical world and digital processing systems.
2. Network Interface Modules
These are specialized interface modules that facilitate communication over LAN, WAN, or wireless networks. Used in routers, switches, and gateways, they’re critical in modern computer hardware infrastructure.
3. Serial Interface Modules
Serial communication is still prevalent in embedded systems and industrial applications. RS-232, RS-485, and UART-based modules provide reliable serial connectivity.
4. Fieldbus Interface Modules
For industrial automation, Fieldbus protocols like PROFIBUS, DeviceNet, and Modbus RTU are standard. Interface modules for these protocols allow control systems to communicate with field-level devices.
5. USB and PCI Interface Modules
These modules expand the capabilities of a computer through ports or slots. USB interface modules connect peripherals, while PCI interface cards extend the hardware’s internal capabilities.
Interface Modules in Industrial Automation
In industrial settings, interface modules are critical for bridging the gap between operational technology (OT) and IT hardware. PLCs, HMIs, and SCADA systems rely on interface modules to control machinery and monitor processes in real-time.
Benefits in Industrial Applications:
-
Fast data transmission between devices
-
Reliable signal integrity under harsh conditions
-
Easy maintenance and hot-swapping of modules
-
Reduced downtime with modular diagnostics
Companies using complex control systems depend on interface modules to connect thousands of I/O points across factories or plants.
Interface Module and IT Hardware Integration
Modern IT hardware design is moving toward modular, scalable systems. Interface modules are at the center of this transformation. Whether in rack-mounted servers, edge devices, or hybrid cloud systems, these modules enhance interoperability and data exchange.
Examples:
-
A network interface module can provide an additional 10Gbps Ethernet port to a blade server.
-
A USB interface module may enable data logging for a sensor array connected to a local workstation.
-
Digital I/O modules expand automation systems in manufacturing floors with minimal reconfiguration.
Benefits of Using Interface Modules
1. Modularity and Scalability
Systems built with interface modules are easier to scale. Need more I/O points? Just add another module. Need a different communication protocol? Swap the existing module for a compatible one.
2. Time-Saving Installation
Plug-and-play functionality, standard connectors, and software auto-detection make installation and configuration much quicker, especially in computer hardware environments.
3. Improved Maintenance and Troubleshooting
Modular systems with interface modules allow quick isolation of faults. Diagnostic LEDs, removable terminal blocks, and status reports simplify troubleshooting.
4. Enhanced System Performance
High-speed communication and reliable signal processing ensure minimal lag, noise, or data loss, making interface modules ideal for real-time systems.
Applications of Interface Modules Across Industries
1. Data Centers
Interface modules in servers and switches allow for redundant network paths, rapid data handling, and flexible configuration for growing demands.
2. Telecommunications
Base stations and switching centers use interface modules to handle different communication standards and protocols across devices and geographic locations.
3. Automotive Systems
Modern vehicles use dozens of interface modules for infotainment, GPS, engine control, and sensor communication. These modules help integrate various ECUs and CAN-bus systems.
4. Smart Cities and IoT
Interface modules connect environmental sensors, surveillance systems, traffic controls, and lighting units to central servers or cloud platforms.
5. Robotics
In autonomous robots, interface modules manage communication between cameras, motor controllers, LiDAR units, and navigation algorithms.
Interface Modules and Computer Hardware Standards
To function seamlessly, interface modules must comply with various hardware and communication standards. Some widely accepted ones include:
-
IEEE 802.x for network modules
-
IEC 61131-2 for programmable controller interfaces
-
USB 2.0/3.0 for peripheral modules
-
PCI Express (PCIe) for internal card-based modules
-
Modbus, CAN, PROFIBUS for industrial protocols
Compliance ensures that interface modules can integrate with legacy systems and new-generation computer hardware platforms alike.
Interface Modules in Cloud-Integrated Systems
Cloud integration has changed how systems communicate. Interface modules now play a dual role: enabling data collection at the edge and ensuring secure transmission to cloud platforms.
Examples include:
-
Smart meters uploading usage data to utility cloud servers.
-
Manufacturing robots sending performance logs for AI analysis.
-
Environmental sensors pushing air quality data to health dashboards.
Cloud-ready interface modules often come with built-in encryption, dual SIMs for redundancy, and over-the-air (OTA) update features.
Emerging Trends in Interface Modules
1. Wireless Interface Modules
As wireless becomes ubiquitous, interface modules now support Wi-Fi, LoRa, ZigBee, and 5G. These are essential for IoT and remote monitoring systems.
2. AI-Enabled Interfaces
AI-ready modules pre-process sensor data at the edge, reducing data loads on central systems. Used in predictive maintenance and anomaly detection.
3. Miniaturization and High Density
As devices shrink in size, interface modules are also becoming more compact. High-density I/O modules now offer dozens of channels within a small footprint.
4. Universal Compatibility
Modern interface modules are being developed with software-configurable channels, allowing them to switch roles or protocols dynamically.
Choosing the Right Interface Module
When selecting an interface module for your IT hardware or computer hardware system, consider the following:
-
Compatibility with your existing devices and protocols
-
Speed and latency requirements for real-time processing
-
Power supply and thermal management
-
Physical space and mounting options
-
Environmental factors like temperature, vibration, and humidity
Always ensure the module supports diagnostics, firmware updates, and integrates easily with control software.
Challenges and Solutions
1. Protocol Mismatches
Using a gateway interface module that supports multi-protocol translation resolves this issue.
2. Limited Expansion
Modular interface racks or backplanes allow you to scale as needed without redesigning the system.
3. Signal Noise and Interference
Modules with built-in filters and isolation circuits minimize interference and maintain data integrity.
Conclusion:
In the realm of IT hardware and computer hardware, connectivity is king. The interface module is more than just a piece of hardware—it is the silent enabler of seamless communication, data integrity, and system harmony.
As the demand for automation, remote monitoring, and cloud computing grows, the role of interface modules will only become more prominent. From industrial floors to smart homes, from data centers to autonomous vehicles, these small but powerful devices will continue to bridge the gap between diverse systems and future technologies.
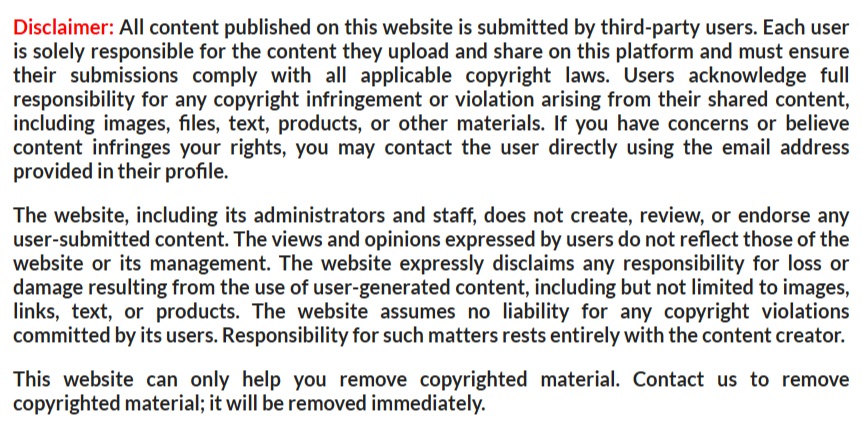
Comments
0 comment