views
Modern engineering pushes boundaries. We design lighter aircraft, more efficient energy systems, safer medical implants, and smarter electronics. But testing these innovations physically? Quite frequently, these actions are too expensive, take an enormous amount of time or are simply impossible. Here, Finite Element Analysis (FEA) comes into play, and ANSYS is a leader around the world in this area.
Mastering sophisticated tools like ANSYS is crucial for engineers tackling these frontiers. For students and professionals navigating the steep learning curve, resources like ANSYS assignment help provide valuable guidance, clarifying complex concepts and accelerating the journey to proficiency. This post delves into the advanced ways ANSYS FEA conquers engineering complexity.
What Makes Engineering Problems Truly Complex?
Not all challenges are created equal. Simple calculations often suffice for basic components. But modern engineering demands solutions for systems where multiple factors collide, creating intricate puzzles:
-
Intricate Geometries: Think turbine blades with complex cooling channels, intricate bone scaffolds for implants, or crumple zones in cars. Modelling these shapes accurately is far beyond simple hand calculations.
-
Multiple Physics Interacting (Multiphysics): Does heat from an engine warp its casing and affect airflow? Does an electric current heat a component and induce structural stress? Real systems rarely experience just one type of physics in isolation.
-
Nonlinear Behaviour: Materials don’t always stretch proportionally to load (plasticity). Components make contact and slide. Large deformations change how forces are applied. Solving equations becomes significantly more difficult due to these nonlinearities.
-
Complex Material Behaviour: Materials aren't perfectly elastic. Think of composites, foams, biological tissues, or materials under extreme temperatures, their behaviour is complex and often anisotropic (direction-dependent).
-
Scale & Computational Demand: Modelling millions of elements for high-fidelity results requires immense computational power and sophisticated solving techniques.
Seeking clarity from a knowledgeable assignment helper online can be a strategic step in mastering specific techniques or troubleshooting complex model setups, ensuring robust and reliable results.
How ANSYS FEA Conquers Complexity: Advanced Capabilities
ANSYS doesn't just do FEA; it provides a comprehensive, integrated environment packed with advanced technologies specifically engineered to tackle the toughest simulation challenges head-on. Here’s how:
Mastering Geometry & Meshing
Before solving anything, the geometry must be discretised into finite elements. ANSYS excels here.
-
Robust Geometry Handling: It seamlessly imports complex CAD models, even healing minor imperfections that could trip up other tools. It's integrated SpaceClaim technology allows direct, intuitive geometry modification without needing the original CAD system.
-
Advanced Automated & Adaptive Meshing: ANSYS offers sophisticated algorithms that automatically generate high-quality meshes (hexahedral, tetrahedral, polyhedral) tailored to the analysis type.
-
Specialised Meshing Tools: For specific challenges like thin shells (cars, aircraft skin), fluid-structure interaction interfaces, or crack propagation, ANSYS provides dedicated meshing controls and element types.
Seamless Multiphysics Integration
Real-world problems involve coupled physics. ANSYS is built for this.
-
Native Coupling: Solvers for structural mechanics, fluid dynamics (CFD), electromagnetics, and thermal analysis are tightly integrated within the ANSYS ecosystem (like Mechanical, Fluent, Maxwell).
-
Sophisticated Coupling Schemes: ANSYS supports one-way (e.g., thermal loads driving stress) and two-way coupling (e.g., fluid pressure deforming a structure which then alters the fluid flow). It handles transient co-simulation where different physics solvers exchange data at each time step.
-
Unified Workflow: Engineers can set up complex multiphysics scenarios within a single interface (ANSYS Workbench), streamlining the process and reducing errors compared to juggling separate, disconnected tools.
Conquering Nonlinearity
Linear assumptions often fail. ANSYS provides robust nonlinear solvers.
-
Material Nonlinearity: Extensive libraries model plasticity, creep (slow deformation under load), hyperelasticity (rubber, polymers), viscoelasticity, and complex composites. Users can define custom material models.
-
Geometric Nonlinearity: Accurately tracks large deformations and rotations, where the shape change significantly affects stiffness and load paths (e.g., inflating airbags, bending sheets of metal).
-
Contact Nonlinearity: Advanced algorithms simulate complex interactions: sliding with friction, separation, sticking, and even wear between multiple components. Meetings, bearings, seals, and collision situations all depend on this.
Advanced Material Modelling
From carbon fibre to human bone, materials behave uniquely.
-
Extensive Material Library: Large built-in libraries with verified properties for metals, polymers, composites, foams, concrete, soils, and biomolecules are available in ANSYS.
-
Sophisticated Composite Modelling: Professional tools (ANSYS Composite PrepPost) use sophisticated parameters (Tsai-Wu, Puck, LaRC) to anticipate failures and create complicated layered structures (ply patterns, angles).
-
User-Defined Materials (UDM): For highly specialised or research-grade materials, engineers can code their constitutive models using APIs.
-
Anisotropy & Temperature Dependence: Accurately models materials whose properties change with direction (like rolled metals or composites) and temperature (crucial for engines, electronics).
Leveraging High-Performance Computing (HPC)
Complex models demand serious computational muscle.
-
Distributed Memory Parallelism (DMP): Splits the model across multiple cores/nodes in a cluster, drastically reducing solve times for large problems.
-
Shared Memory Parallelism (SMP): Utilises multiple cores on a single machine efficiently.
-
GPU Acceleration: Offloads computationally intensive tasks to powerful graphics processors for significant speedups, especially in explicit dynamics (like crash simulation).
-
Cloud Scalability: Easily deploy simulations to cloud computing resources via ANSYS Cloud, providing on-demand access to virtually limitless HPC power without heavy local infrastructure investment.
Robust Solver Technology
The core solvers are the workhorses. ANSYS invests heavily here.
-
Diverse Solver Arsenal: Offers direct solvers (robust for smaller, ill-conditioned problems) and highly efficient iterative solvers (like PCG, ICCG, sparse) optimised for large-scale models.
-
Explicit Dynamics (ANSYS LS-DYNA, AUTODYN): Specialised solvers for extremely fast, transient events like impacts, explosions, and crashworthiness where inertial effects dominate. These use explicit time integration schemes.
-
Solver Diagnostics & Control: Provides detailed feedback and controls to help engineers troubleshoot convergence issues and fine-tune solver parameters for maximum efficiency.
Conclusion
Finite Element Analysis with ANSYS is far more than a digital replacement for physical testing. It's a transformative engineering paradigm. ANSYS FEA provides valuable information about the real behaviour of products and systems by dealing with complicated designs, combining numerous types of physics, controlling strong nonlinearities, modelling all types of materials, leveraging advanced computing and using trustworthy solutions.
These benefits include greatly cut development costs and time spent launching products, much better and reliable products, a reduced risk from prototyping and openness to explore designs never before possible.
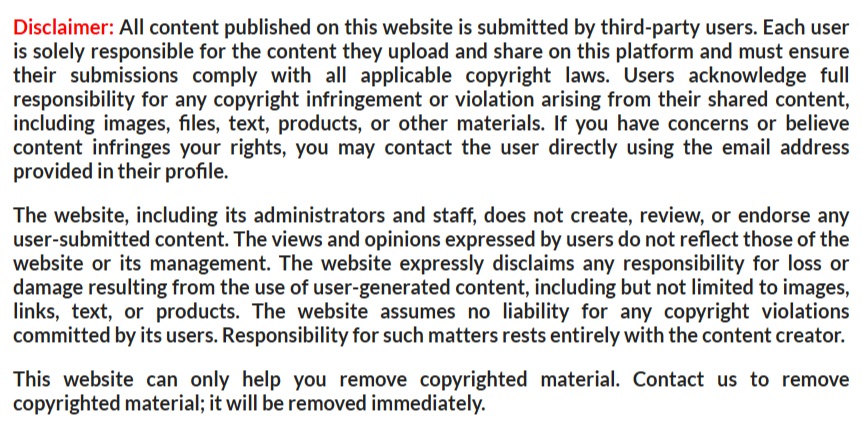
Comments
0 comment