views
Workplace Accident Investigation:
Workplace Accident Investigation:
There are many elements that must be collected for a truly thorough workplace accident investigation.
Regardless of how small or seemingly insignificant they may be, every element needs to be identified, photographed, listed or marked in some way so that it can be valuable in the “big picture” of the investigation. Click here incident investigation course
What should you do first?
How deeply should you investigate the details? In this post, we have gathered information on several easy-to-use investigation tools that can be used or adapted to your own accident investigation plan.
Proper investigation procedures will help you:
a) Identify the evidence.
b) Identify the factors that contributed to the accident.
c) Photograph or sketch the accident scene.
d) Take notes.
e) Interview witnesses.
Identify the Evidence:
Evidence is anything that is real, substantiated and can help clarify the facts. Physical evidence can be seen, felt and even tasted. It can be large or small, solid or liquid.
The identification and collection of evidence helps determine the fundamental cause of the accident. Evidence may include the following:
a) Position of equipment and tools.
b) Air quality in the accident area.
c) Cleanliness and maintenance of equipment and tools.
d) Condition of the floor, pavement or surface.
e) Equipment maintenance records.
Position of Equipment and Tools:
The position of equipment and tools at the accident site can provide information about how they were being used before the event. This can help determine whether incorrect use of equipment was one of the causes of the problem.
Air Quality:
If there is a suspicion that the air quality in the workplace or nearby may have contributed to causing the accident, it is essential to investigate it.
Through this process, we can obtain valuable information regarding the control of environmental conditions carried out by Safety Engineering, as well as the concentrations of contaminants that are above the Exposure Limits.
Among the specific elements that must be evaluated when monitoring air quality are:
a) Oxygen.
b) Carbon monoxide.
c) Aerosols.
d) Gas and vapor emissions.
If it is concluded that atmospheric conditions may have contributed to causing the accident, it is necessary to evaluate the engineering controls and to conduct studies aimed at improving air quality in the location and in the environment as a whole.
To reinforce the effectiveness of an investigation, we can include checking:
a) Lighting.
b) Visibility limitations due to the presence of dust, smoke and mist.
c) Excessive noise levels.
d) Reasons that may attract the worker's attention, distracting him/her.
Cleaning and Maintenance of Equipment and Tools:
Poor cleaning and inadequate maintenance of equipment and tools can also contribute to the cause of workplace accidents.
A thorough investigation also examines whether chemical residues, dirt, equipment operating conditions and the quality of the tools contributed to the occurrence of the accident.
Floor Conditions:
Floor conditions are another risk factor for accident hazards. For this reason, the floor must always be kept dry, free of residues or defects (such as holes, protruding objects, etc.).
Surfaces must be wide enough to allow free movement of people and mobile equipment, such as forklifts, for example. The investigation should include questions such as:
a) Was the work surface dry and in good condition?
b) Was it slippery, dirty with grease or oil?
c) Does the work area allow free movement of equipment and people?
d) Is the floor covered with non-slip material to prevent falls?
Identify the factors that contributed to the accident
In addition to physical evidence, there may be other factors that contribute to an accident. These include operational failures, violation of standards and procedures, state of mind, health history, misuse of medications, drinks, etc.
Operational failures occur during normal work activities and are often among the main causes of accidents.
a) mechanical equipment without protective devices;
b) defective or deficient protective devices;
c) defective/damaged scaffolding, ladders, tools or electrical equipment;
d) handling of gases, vapors and liquids without due care;
e) inadequate ventilation or lighting;
f) excessive exposure to noise, etc.
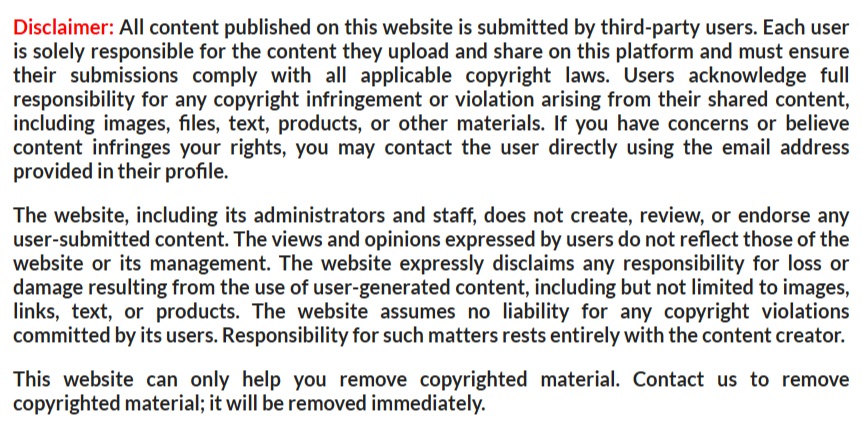
Comments
0 comment