views
In the rapidly evolving world of additive manufacturing, one material has stood out for its unique balance of strength, flexibility, and durability: nylon. While there are many materials used in 3D printing, nylon 3D printing has become increasingly popular across industries for both prototyping and functional parts.
In this article, we’ll explore the many benefits of nylon 3D printing, examine its key properties, and explain why it’s an excellent choice for a variety of applications.
What is Nylon 3D Printing?
Nylon, also known as polyamide, is a synthetic polymer known for its toughness and versatility. When used in 3D printing, nylon is typically offered as:
-
Nylon filament for FDM (Fused Deposition Modeling) printers
-
Nylon powder for SLS (Selective Laser Sintering) systems
These forms allow for different types of 3D printing processes, each suited to particular needs and applications.
Key Properties of Nylon for 3D Printing
Why choose nylon for 3D printing? Here are some of its standout properties:
1. High Strength and Durability
Nylon has excellent tensile strength, making it ideal for parts that need to withstand mechanical stress. It’s used in functional prototypes and end-use parts where reliability is essential.
2. Flexibility and Impact Resistance
Unlike brittle plastics like PLA, nylon offers a good balance of flexibility and toughness. It can absorb impacts without breaking, making it perfect for components that need to endure wear and tear.
3. Low Friction and Good Abrasion Resistance
Nylon’s low friction coefficient and wear resistance make it ideal for applications like gears, bushings, and bearings.
4. Lightweight
Nylon is relatively lightweight compared to metals and some other plastics. This is important for industries like automotive and aerospace, where weight reduction can improve efficiency and performance.
5. Chemical Resistance
Nylon is resistant to many chemicals, including fuels, oils, and solvents. This property expands its use in industrial environments.
6. Thermal Stability
Nylon has a higher melting point than many other 3D printing plastics, allowing it to perform well in applications exposed to moderate heat.
Advantages of Nylon 3D Printing
Let’s explore how these properties translate into practical benefits for 3D printing.
High Mechanical Performance
The strength and flexibility of nylon make it suitable for parts that need to bend without breaking. This is particularly useful for functional prototypes, jigs and fixtures, and even some end-use components.
Excellent Surface Finish
Nylon prints generally produce smooth, matte finishes, which can be further refined through post-processing like polishing or dyeing. This professional finish makes nylon parts attractive for both functional and cosmetic uses.
Versatility for Prototyping and Production
Thanks to its durability and mechanical properties, nylon 3D printing can bridge the gap between prototype and production. Businesses can test designs and move to small-batch production runs without retooling or switching materials.
Common Applications of Nylon 3D Printing
Nylon’s unique properties lend themselves to a wide range of applications, including:
Engineering and Mechanical Parts
Nylon is often used to create:
-
Gears and pulleys
-
Bearings and bushings
-
Tooling and jigs
-
Mechanical housings
These parts benefit from nylon’s impact resistance and low friction.
Automotive Components
Automakers use nylon 3D printing to create:
-
Custom air ducts and fluid reservoirs
-
Clips, fasteners, and brackets
-
Prototyped interior components
Lightweight nylon parts can reduce vehicle weight, improving fuel efficiency.
Consumer Goods
Nylon’s attractive finish and strength make it popular in:
-
Sporting goods (bike components, helmets)
-
Wearables and accessories
-
Household items
Medical and Dental Devices
In medical applications, nylon is used for:
-
Custom braces and orthotics
-
Surgical guides
-
Prototyped medical device housings
Its biocompatibility and durability make it well-suited to these uses.
Nylon 3D Printing Techniques: FDM vs. SLS
Nylon 3D printing can be achieved through different technologies. The two most common are FDM and SLS. Here’s a quick comparison:
FDM (Fused Deposition Modeling)
-
How it works: A heated nozzle extrudes nylon filament layer by layer.
-
Advantages: Affordable, easy to set up, accessible for small businesses or home use.
-
Drawbacks: Nylon filament can be prone to warping without a heated build chamber.
SLS (Selective Laser Sintering)
-
How it works: A laser fuses nylon powder layer by layer to create solid parts.
-
Advantages: No support structures needed (the powder acts as support), better dimensional accuracy, and excellent mechanical properties.
-
Drawbacks: More expensive and requires professional-grade equipment.
Choosing between FDM and SLS depends on your project’s needs, budget, and desired quality.
Tips for Successful Nylon 3D Printing
Working with nylon can present some challenges. Here’s how to ensure the best results:
1. Control Moisture
Nylon is highly hygroscopic—it absorbs moisture from the air. Moisture can cause poor layer adhesion and surface imperfections.
-
Store filament or powder in a dry environment.
-
Use filament dryers or preheat powder before printing.
2. Optimize Print Settings
-
Higher printing temperatures (around 240–260°C for FDM nylon).
-
Heated bed (at least 60°C) to reduce warping.
-
Enclosed build chamber (for FDM) to maintain consistent temperature and reduce warping.
3. Post-Processing
-
Polishing: Improve surface smoothness and aesthetics.
-
Dyeing: Nylon parts can be dyed to achieve custom colors.
-
Annealing: Some nylon prints can be heat-treated to improve strength.
The Environmental Impact of Nylon 3D Printing
Sustainability is a growing concern in manufacturing. Nylon, like many plastics, can pose challenges if not handled responsibly. Here’s how the 3D printing industry is addressing this:
-
Recyclable powders and filaments: Some SLS powders are reusable for multiple prints, reducing waste.
-
Lightweight designs: Nylon parts can reduce the weight of vehicles or products, contributing to lower energy use in the final application.
-
Localized production: 3D printing on-demand minimizes shipping and inventory waste.
While not biodegradable, nylon’s long lifespan can also reduce the need for frequent replacements.
Nylon 3D Printing vs. Other 3D Printing Materials
How does nylon compare to other popular 3D printing materials?
PLA (Polylactic Acid)
-
PLA: Easy to print, biodegradable, but brittle and less heat-resistant.
-
Nylon: More flexible, durable, and heat-tolerant, making it better for functional parts.
ABS (Acrylonitrile Butadiene Styrene)
-
ABS: Tough and heat-resistant but prone to warping.
-
Nylon: Tougher and more flexible, with better wear resistance.
PETG (Polyethylene Terephthalate Glycol)
-
PETG: Good impact resistance, less prone to warping than ABS.
-
Nylon: Offers greater mechanical strength and lower friction.
Why Nylon 3D Printing is Gaining Popularity
Industries are increasingly turning to nylon 3D printing for these reasons:
-
Versatility: It’s suitable for both prototypes and production parts.
-
Durability: High impact strength and flexibility make it reliable in tough applications.
-
Cost-effectiveness: Especially in SLS, parts can be produced quickly and affordably compared to machining or molding.
-
Customization: Parts can be tailored to specific projects or user needs.
Final Thoughts: Harnessing the Power of Nylon 3D Printing
Nylon 3D printing has firmly established itself as a go-to solution for durable, functional parts across industries. From engineering and automotive applications to medical devices and consumer goods, nylon’s unique blend of strength, flexibility, and lightweight design has opened new doors for manufacturers and innovators alike.
Whether you’re a designer prototyping a new product or an engineer seeking a reliable end-use part, nylon 3D printing offers the performance and versatility to bring your ideas to life.
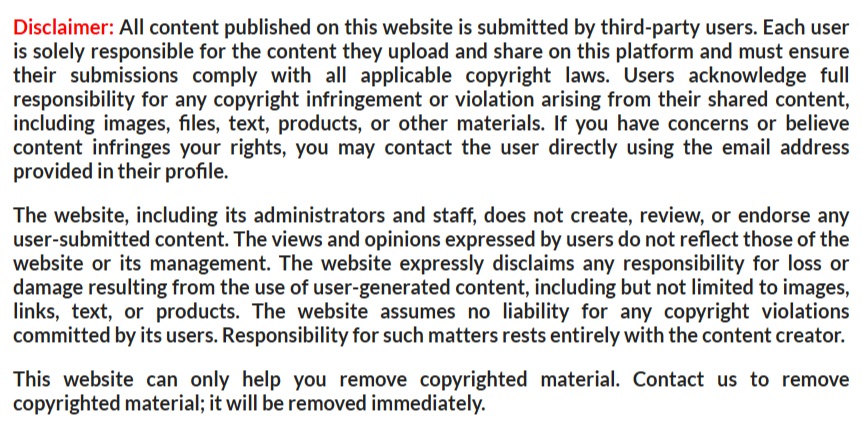
Comments
0 comment