views
Acoustic Material Industry Cutting Machines: Precision Tools for Soundproofing Innovation
As modern construction, automotive, and electronics industries increasingly prioritize noise control, the demand for acoustic materials — such as foam, fiber, composite panels, and sound-damping sheets — continues to grow. But turning large rolls or sheets of acoustic insulation into precise, application-ready components requires specialized equipment: Acoustic Material Industry Cutting Machine.
These cutting machines are engineered to handle soft, flexible, and often fibrous materials with accuracy and speed. Whether you’re producing soundproofing panels for buildings or interior noise insulation for vehicles, the right cutting solution ensures clean edges, consistent dimensions, and minimal material waste.
This article explores the types of cutting machines used in the acoustic material industry, their key features, applications, material handling challenges, and how to choose the best one for your needs.
1. The Role of Acoustic Materials in Industry
Acoustic materials are engineered to absorb, block, or dampen sound. They are commonly used in:
-
Architectural and building construction (walls, ceilings, floors)
-
HVAC systems (duct linings)
-
Automotive interiors (door panels, headliners, engine compartments)
-
Appliances and electronics (reducing mechanical noise)
-
Industrial machinery (soundproof enclosures)
These materials vary widely in composition — from soft PU foam and fiberglass to denser composites with metal or polymeric layers — making cutting accuracy and adaptability critical in production.
2. Types of Acoustic Material Cutting Machines
Different machine types cater to different production needs and material characteristics:
2.1 CNC Oscillating Knife Cutting Machines
These are the most common cutting systems for acoustic materials. The oscillating knife moves rapidly up and down, allowing it to slice through soft materials like foam and fiber with clean, precise edges.
Advantages:
-
High precision and repeatability
-
Suitable for multi-layer cutting
-
Works on a wide range of materials
-
Ideal for 2D cutting shapes with complex contours
2.2 CNC Laser Cutting Machines
Laser cutters are occasionally used for specific acoustic materials like polyester fiberboard or thin polymer layers.
Advantages:
-
Extremely clean cuts with sealed edges
-
No physical contact – less wear
-
Fast cutting speed for thin materials
Limitations:
-
Not ideal for thick foam (melting or burning risk)
-
Fumes may require extraction systems
2.3 Waterjet Cutting Machines
Waterjet cutters use a high-pressure jet of water (sometimes with abrasive additives) to slice through dense or layered acoustic panels.
Advantages:
-
No heat – prevents material deformation
-
Excellent for composite or metal-backed acoustic materials
-
Cuts through thick, rigid materials with ease
Limitations:
-
Higher operating costs
-
Requires water and drainage infrastructure
2.4 Die Cutting and Hydraulic Press Machines
For high-volume production of standard parts, die cutting machines using hydraulic presses are still common.
Advantages:
-
Fast, batch-oriented production
-
Low cost per part once tooling is made
Limitations:
-
Requires tooling for each shape
-
Not ideal for short runs or custom parts
3. Common Acoustic Materials Processed
Acoustic cutting machines are designed to handle a wide range of soundproofing materials, such as:
4. Key Features of Acoustic Material Cutting Machines
Modern cutting machines for the acoustic industry often include:
4.1 Automated Nesting Software
-
Maximizes material usage by laying out patterns to reduce waste.
-
Helps lower production costs.
4.2 Vacuum Hold-Down Tables
-
Secures lightweight or compressible materials during cutting.
-
Prevents shifting and improves edge quality.
4.3 Multi-Tool Heads
-
Allows cutting, creasing, punching, and marking in one pass.
-
Ideal for complex or multi-layer materials.
4.4 Vision or Registration Systems
-
Detect printed marks or pre-cut templates.
-
Ensures accurate cutting alignment, especially in printed acoustic panels.
5. Applications and Industries
Cutting machines tailored for acoustic materials serve a range of sectors:
5.1 Building & Construction
-
Cutting ceiling tiles, wall panels, floor underlays, and duct liners.
5.2 Automotive
-
Producing acoustic insulation for doors, dashboards, trunk liners, and engine bays.
5.3 Appliance Manufacturing
-
Custom-fitting insulation pads for washing machines, refrigerators, and HVAC units.
5.4 OEM Soundproofing Suppliers
-
Contract manufacturers producing parts for multiple industries.
6. Challenges in Cutting Acoustic Materials
Acoustic materials pose unique challenges:
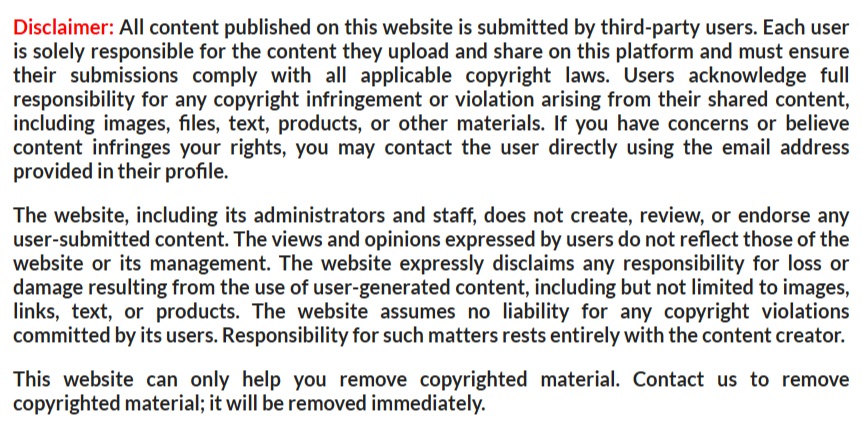
Comments
0 comment